Introduction
Introduction by General Manager
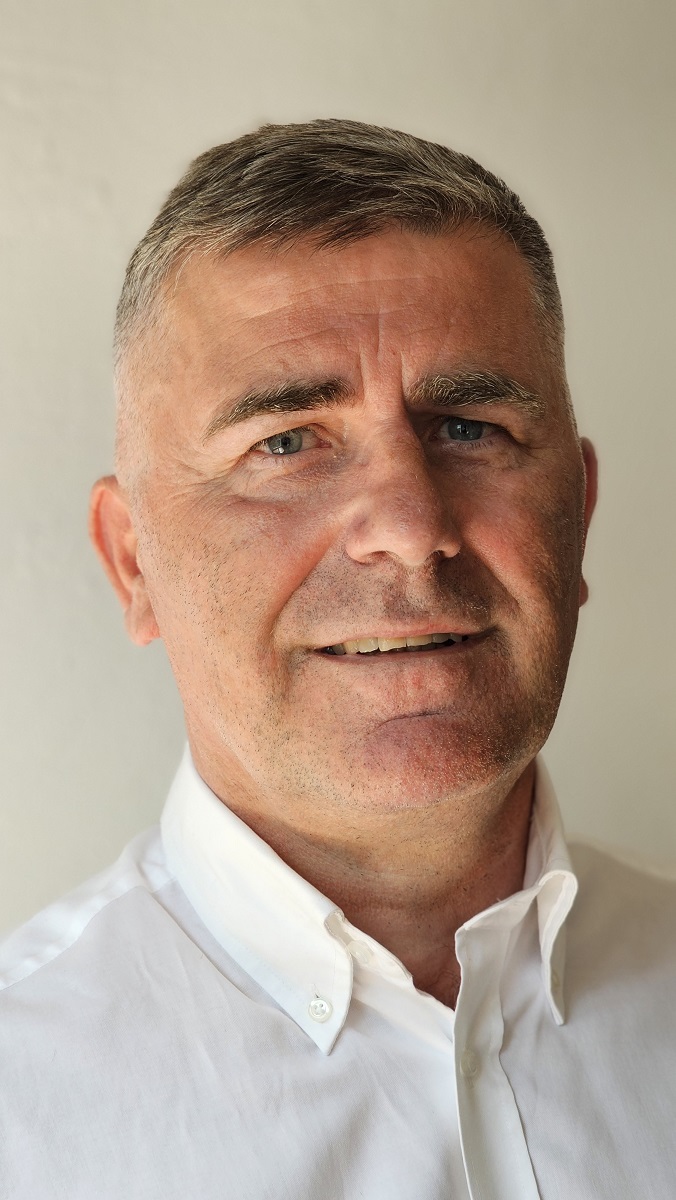
ZVU Engineering a.s. is from its establishment a direct successor of more than 150-year tradition of machinery production of ZVU and its legal predecessors. Since the First Czech Joint-Stock Machinery Works was founded in 1869, the Company has been manufacturing machines and equipment for food and chemical industries, both for domestic and export markets. In 20th century this program was expanded also in manufacturing and delivery of process units and plants for power and ecology industries.
At competing on markets, ZVU Engineering focuses on deliveries with a higher added value of engineering activities. Main strategy applied consists in minimizing risks in all stages of project preparation and implementation, both from the client´s and ZVU Engineering points of view. To eliminate risks, qualified and motivated team provides major instrument together with full understanding and professional analysis of the client´s technical and economical requirements, and last but not least with the accumulated know-how of ZVU Engineering and its legal predecessors in given branch. As an example, the mentioned know-how can be presented by more than 1.6 million drawings placed in company archives.
The Company makes efforts to build long-term partnership, both with the clients and suppliers. We are persuaded such an attitude facilitates cooperation significantly, namely in so complicated branch represented undoubtedly by capital investments. We always try to provide a potential client with full assistance needed for preparation of its intention, either in form of elaborating an appropriate study, technical evaluation or a special offer. The aim of that procedure is entire understanding of the client´s needs and minimizing occurrence of eventual misunderstanding during the project implementation course, related to maintaining the cost budget and reaching the designed parameters. Detailed knowledge of price levels of process plants, its components and subcontractor’s activities in investment engineering allow ZVU Engineering to prepare qualified cost, technical and economic studies and quotations. At the same time ZVU Engineering continues to utilize synergy advantages resulting from financial, proprietorial and manufacture-technical background of ZVU Group. Affiliation to the group with manufacturing background is of beneficial effect both with regard to practical development of designers and engineers, who have a chance to follow and check implementation of their design works, and with regard to access to information related to manufacturing costs and technological procedures.
Our company position is based on the mentioned long-term tradition and exclusive knowledge resulting from that, for example in the field of coke oven chemistry, nitric acid production, pressure coal gasification, heat exchange and others. The company takes care of the know-how advancement by permanent implementation of research and development tasks. The tasks are focused on effectivity and ecology improvements of the solutions offered by us. The company dedicates a lot of its technical and marketing capacities to the research and development activities.
The high quality of all deliveries and services obvious at present in highly competitive economy is a necessary precondition. In case of ZVU Engineering, taking into consideration deliveries of pressure equipment, the high quality is absolute condition. For a long time introduced quality system, in accordance with ISO 9001 standard series, has been extended by passing to quality management system according to ISO 9001:2009 standard. Since October 2022 the international standard for Environmental Management Systems and the international standard for Occupational Health & Safety (OH&S) Management Systems has been impelmented and certified in accordance with the ISO 14001:2015 a ISO 45001:2018.
- Engineering, delivery, construction and commissioning of Flue Gas Desulphurization Plant in Power Plant Prunéřov II (Czech Republic), supported by Mitsubishi (Japan) process, put in operation in 1996.
- Hydrogen production plant in Slovnaft a.s., Bratislava (Slovakia), supported by Chyioda (Japan) process, put in operation in 1999.
- Heavy tar condensate separation and sealing, Heavy Tar Condensation CB No. 9 in Coke Oven Plant Svoboda in Ostrava (Czech Republic), put in operation in October 2002.
- Reconstruction of absorption unit in the production plant BorsodChem-MCHZ, s.r.o., in Ostrava (Czech Republic) with capacity of 220 t/day of nitric acid (100%), put in operation in March 2003.
- Hydrogen production unit in BorsodChem-MCHZ, s.r.o., in Ostrava (Czech Republic), with a capacity of 6,000 Nm3/hour, based on Haldor Topsøe (Denmark) process, put in operation in August 2005.
- Extended basic design based on our own process and delivery of coal pressure gasifiers and critical items for construction of Coal Pressure Gasification Plant of energy gas production 40.000 Nm3/h; construction of the Plant started in 2004, the Plant was put into operation in March 2007, client SUZMK ENERGO (Russia).
- Detail engineering and supervision for VAIF Ltd. (Finland) in construction of the Coke Oven Battery By–Product Plant Modernization Project, Isdemir (Turkey) in 2006 and 2007.
- Revamp of the final absorber and retrofit of the de-monomer columns in Spolana a.s. (Czech Republic) in 2006.
- Hydrogen production units with a capacity 5,000 Nm3/h, 30,000 Nm3/h and 26,000 Nm3/h for Haldor Topsøe (Denmark), delivered in 2006, 2009, 2012 and 2020.
- Gas cooling unit for Pressure Gasification Plant Vřesová (Czech Republic), with capacity of 135,000 Nm3/hour of raw gas, put in operation in October 2007.
- Biogas treatment unit (siloxanes removal upstream of the cogeneration unit) for PVK a.s. Prague (Czech Republic), put in operation in December 2007.
- Waste heat boiler of II grade for ammonia production Plants in Russia with gas capacity 332,000 Nm3/h, delivered in September 2007.
- Revamp of Sulphur dioxide production plant, capacity 5.1 t/h sulphur, for Spolana a.s. (Czech Republic), put in operation in June 2010.
- Converter including steam boiler for nitric acid plant in Lovochemie put in operation in August 2011 and in Synthesia put in operation in August 2011 (both Czech Republic).
- COG Final cooler for HP Frýdek- Místek, put in operation at Coke Oven Plant Arcelor Mittal Ostrava (Czech Republic) in June 2012.
- Wash oil still for TŽ Třinec (Czech Republic), put in operation in December 2012.
- Steam boiler for nitric acid plant in BorsodChem-MCHZ, s.r.o., Ostrava (Czech Republic), put in operation in September 2013.
- Detail engineering and deliveries of Benzole scrubber for HP Frýdek- Místek, installed in OKK a.s., Coke Plant Svoboda, Ostrava (Czech Republic), put in operation in August 2013.
- Wash oil still integrated with Regenerator and Collecting vessel for Koksoprojekt Zabrze (Poland), installed in Coke Plant Pryjazń, Dąbrowa Gornicza (Poland), put in operation in October 2014.
- Gas cooler for Lučební závody Draslovka a.s., Kolín (Czech Republic), put in operation in November 2014.
- Wash oil still integrated with Regenerator and Collecting vessel for Koksoprojekt Zabrze (Poland) – put in operation in 2015.
- EPC project Substitution of solvent cresol for MNP, client Paramo a.s. Pardubice (Czech Republic) – put in operation in 2015.
- 9 Experimental Units for Experimental Base of the Unipetrol Research & Educational center within the program UniCRE, handed over in 2016 to Unipetrol RPA, Litvinov, Czech Rep., 1 experimental unit set for hydrocracking simulation in March 2020.
- New N30A/B Boiler internals for Nitric Acid Production Line 2 for Duslo, Šaľa, Slovakia, put in operation in August 2016.
- Denitration Column in Nitric Acid Production Line for customers Lovochemie a.s. and Synthesia a.s. in the fall of 2016 and in the spring of 2021.
- Adiabatic Nitrobenzene Unit for BorsodChem MCHZ, s.r.o., Ostrava, put in operation by the end of 2021.
The above indicated references prove best our contracting portfolio, our lodgment on the market and ability to meet flexibly and reliably clients’ requirements. Maintaining and development of these capabilities is the main goal as well as the best guarantee for future prosperity.
![]() |
|
Pavel Simajchl
General Manager
|